Innovation in extrusion technology
The demand for innovations that lead to higher product quality increases the pressure on extrusion companies to invest in modern technologies. Extrunet develops customized solutions based on customer requirements and listens carefully to pinpoint the exact pain points. Your problem drives us forward! Impossible is not an option!
extrunet loves the challenge!
Flexible solutions
As a provider of systems and tools for profile extrusion with decades of experience, we offer a well-thought-out standard program. However, we see ourselves as a solution provider with high flexibility in tool and machine construction. Projects from the concept phase to the finished plastic profile are our daily business.
Solutions for post-processing
For us, the overall process does not only include extrusion. We are also your competent partner for inline processing of profiles – punching, milling, automatic stacking, and much more.
Our strong partners for secure automation technology
Our sister companies codeSec and codeTec combine operation technology (OT) and the most modern automation solutions for extrusion technology. While codeSec specialises in IT and OT security, codeTec provides state-of-the-art control technologies and PLC programming. Together, we offer you integrated and secure solutions for your production processes.
Your Benefits with an extrunet extrusion system
-
Easy Compliance with Tolerance Levels
Extrunet extrusion systems are fully digitally controlled and regulated – with extrunet systems, you can store and retrieve your profile specifications. Using digital options (also retrofittable for existing systems), the extrusion system automatically takes measures to keep your profile within tolerance.
Automatic Deviation Correction
Through cooling or heating – e:MAC-d – defined profile sections are kept within tolerance during production. Deviations of up to +/- 0.2mm can be compensated. In combination with an inline measurement system, a closed-loop control circuit can be realized.
Automatic Product Sorting
Integrated profile measurement methods detect surface defects. With our integrated profile measurement methods e:PMC(Laser sensors or camera systems) and is automatically sorted into good and reject material.
Perfect Surfaces
With our integrated gloss heating in the nozzle, the surface gloss can be optimized.
Prevention of Deposits
The digitally controlled cooling in the nozzle regulates individual profile sections and prevents material from sticking, thereby avoiding long production interruptions due to cleaning.
Contour-specific air application – e:MAC-c - at the nozzle outlet counteracts blade out and extends production cycles. This means no blade out, wax deposits, or burr formation.
No Problem with Thrust Changes
The gravimetric dosing unit controls the material flow. The process is adjusted to the material weight.
Extrunet offers a variety of solutions to avoid this problem.
Quality Transparency - Profile Contains Quality Information
Your product is timestamped and remains transparent up to controlling.
The patented Profile Sample Assistant – e:PSA – not only significantly reduces inspection times but also automatically assigns all process data to the profile sample. This makes continuous quality control easy.
-
Reproducibility
Standardized and digitally supported processes make your production independent of individual know-how.
With our positioning system – e:TPS – all calibration table positions are stored profile-related in the recipe management – ensuring reproducible settings.
Intelligent Early Warning Systems
Prevents profile breakage and potential errors before they occur.
With Profile-Breakage-Detection – e:PBD – is continuously measured via the vacuum value in the dry calibrator or the pulling force and compared with the target values. If a change occurs, a signal is automatically issued, and countermeasures are initiated.
With the innovative slip control – e:PSC – the pulling speed is monitored and corrected accordingly in case of deviations.
Continuous and Defined Maintenance Plans
Extrunet's digital solutions enable predictive maintenance – e:PMS (Predictive Maintenance Service) – performing a full functionality check before each production start, detecting defective components, and notifying about upcoming maintenance tasks.
Auto-START and Auto-STOP
Extrunet offers solutions like Auto-START and Auto-STOP. Programmed times allow for automatic heating of the extruder and tool. With Auto-STOP, the line is shut down completely either manually or automatically. This is particularly useful for night shifts with reduced personnel deployment.
Automatic Cooling Water Temperature Control
Fluctuations in cooling water temperature are compensated for, resulting in a stable production process. With the innovative extrunet solution e:MCC – Individual cooling circuits are perfectly regulated using flow control and maintained at the desired setpoint.
In addition to simplified servicing of the tools, this achieves significant cooling water savings. Moreover, defined cooling water volumes can counteract profile bending.
Further Automation Options
Automated calibration and startup assistance
Inline measurement with control loops
Fully automated profile stacking systems
The eqxtru-BOX for highly efficient quality control
A variety of digital solutions for semi-autonomous production
Automated storage system
-
Up to 80% less cooling water consumption with e:MCC
Through automatic cooling water temperature control
Up to 60% less total energy consumption
Save more electrical energy with Vacuum Technology with ECO plus compared to conventional vacuum systems
Minimal material usage through precise process control.
The optimized process saves material, energy, and time, leading to an increase in overall efficiency.
Durable Tools
With a sophisticated technology, nozzles and calibrations are CrNi-coated. This extends service life and makes tool cleaning easier.
Short Setup Times
Quick-change systems and hoseless, simple calibration ensure minimal downtime.
The dies are preheated before assembly. This prevents incorrect connection of the die heaters.
With hoseless calibration, setup becomes effortless – simply place it on, lock it – done. Individual water and vacuum connections are a thing of the past.
Transparent Process Data Storage
Transparent Process Data Storage – e:DIGI – not only stores all process data, giving you the ability to conduct detailed process analyses, but also displays the entire extrusion process live, ensuring perfect control of your production.
With a 100% weight control of profile bars, you not only achieve perfect monitoring but also gain better oversight of your material costs.
e:MAC-d enables you to monitor sensitive profile sections inline and produce at the lower weight tolerance level.
Central Operating Data Collection
Modern extrunet machines collect operating data through a dense network of measuring points.
This data is stored, analyzed, and displayed in a Grafana dashboard. No matter where your machines are located worldwide. With e:DIGI you can conveniently monitor the productivity of your systems from your office chair.
Additionally, all data is stored and can be retrieved even months later – a perfect solution for seamless traceability of process data.
-
Savings & Resource Conservation
By minimizing material usage and achieving significant energy savings through modern cooling water management and optimized vacuum regulation, you reduce your CO₂ footprint.
With extrunet machines, you save:
up to 80% cooling water capacity with e:MCC
Approx. 60% electrical energy compared to conventional vacuum systems with Vacuum Technology with ECO plus
Digital Options
Filter through the great selection
Filter is active
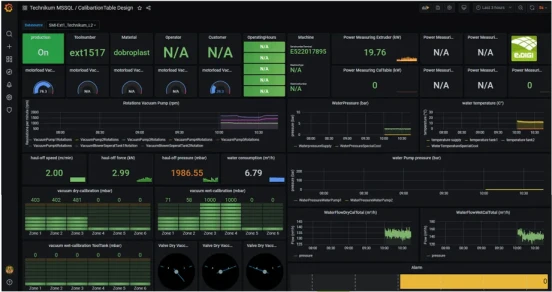
All data of your extrusion process at a glance. For continuous monitoring and evaluations.
The data is stored, analyzed, and displayed in a Grafana dashboard. No matter where your machines are located in the world. With e:DIGI, you can conveniently monitor the productivity of your systems from your desk chair.
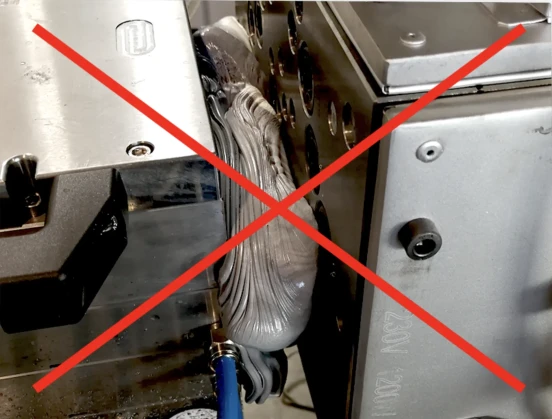
Early warning of profile breakages and partial profile breakages – visually, acoustically, and digitally – already within the dry calibration phase.
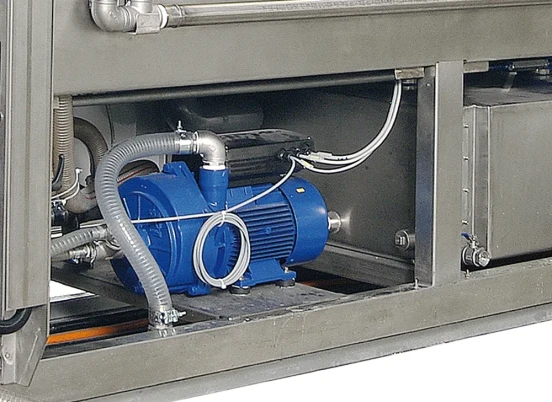
Up to 55% energy savings: Vacuum supply in the dry area with frequency-controlled vacuum pumps, in the wet area with a separation tank including a side channel blower and water pump.
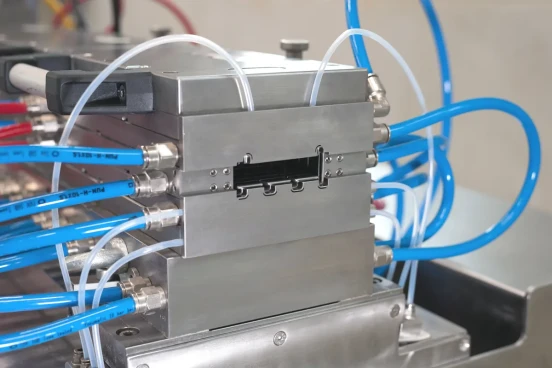
Longer production times, controlled process reliability, higher energy efficiency and optimization of good production through automatic correction of deviations
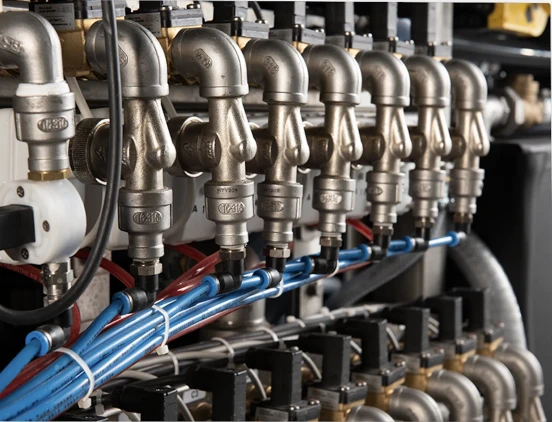
By local cooling, profile dimensions are adapted during ongoing operation. This means for you: Reduction of machine downtimes and capacity losses, stabilization of profile quality and production process, and reduced cooling water consumption.
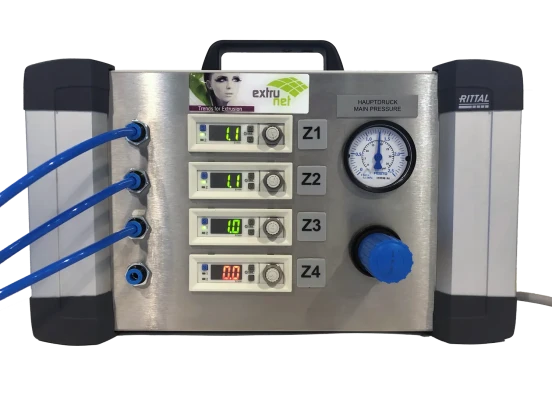
No sticking of internal webs and secure production even for complex multi-chamber profiles.
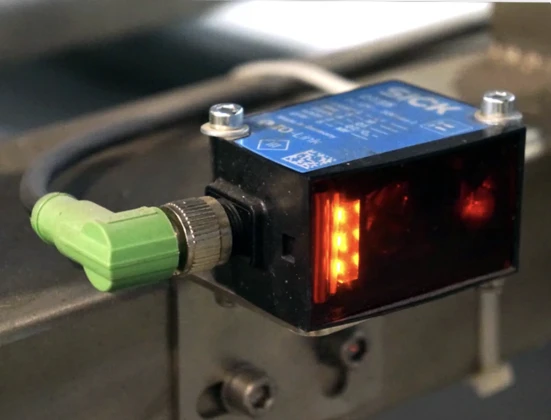
Digitally controlled alignment of the calibration table on all spatial axes. All data is recorded, stored, and can be precisely reproduced for future productions.
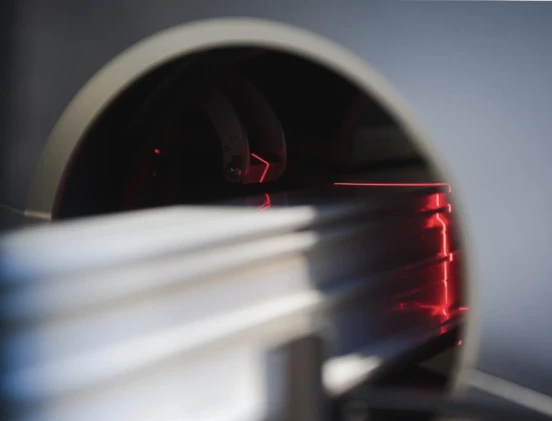
Through precise profile measurement during the production process, the modules for cooling and air control can automatically respond to deviations. Your advantage: higher stability in profile quality and the production process.
In combination with an inline profile measurement, the functions of e:MAC and e:MCC can be used to keep dimensions permanently within predefined limits.
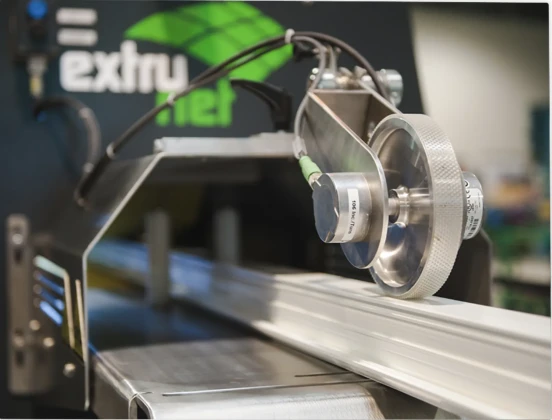
Higher machine utilization and reduction of scrap and downtimes through automatic corrective actions in case of profile slippage.
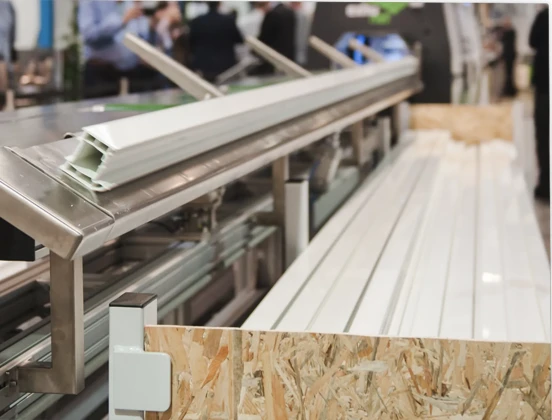
Through precise measurement of profile weight, good production and scrap are automatically separated.
Digital recording of actual profile weight at the tilting table.
Left/right ejection of profiles (separation of production/scrap)